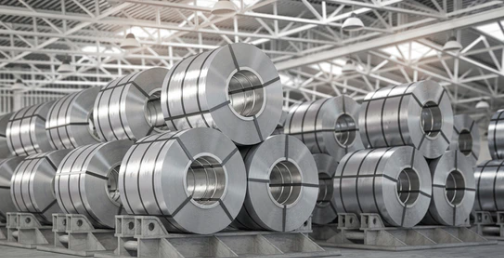
A Complete Guide to Choosing the Right Partner
Introduction: The Importance of Aluminum Coils in Industry
Aluminum coils are crucial components in various industries, serving as the foundation for manufacturing products in construction, transportation, electrical, packaging, and more. Lightweight, corrosion-resistant, and highly conductive, aluminum coils are the backbone for products requiring durability and efficiency. For companies reliant on aluminum coil manufacturer a trustworthy aluminum coil manufacturer is essential to ensure quality, reliability, and performance.
This article explores what sets leading aluminum coil manufacturers apart, detailing their production processes, industry applications, and factors that companies should consider when choosing the right manufacturing partner.
Key Properties of Aluminum Coils
Aluminum coils possess unique properties that make them suitable for a broad range of applications:
- Lightweight: At about one-third the weight of steel, aluminum is an ideal material for applications where weight reduction is critical.
- Corrosion Resistance: Aluminum naturally forms a protective oxide layer, which prevents rust and extends the life of the material.
- High Thermal and Electrical Conductivity: Aluminum is a great conductor of heat and electricity, making it ideal for applications in heating, cooling, and electronics.
- Reflectivity: Aluminum’s reflective surface makes it valuable for lighting and insulation applications.
- Malleability: It can be shaped, cut, and molded into complex designs without compromising structural integrity.
Manufacturing Process of Aluminum Coils
To create high-quality aluminum coils, manufacturers must follow a precise and controlled manufacturing process, ensuring consistency, durability, and industry compliance. Here are the key steps involved:
1. Melting and Casting
The process begins with melting raw aluminum or recycled aluminum scrap in large furnaces. Once molten, it’s cast into solid slabs, known as ingots, which serve as the base for coils.
2. Hot Rolling
The aluminum ingots are heated to a high temperature and passed through a rolling mill, which reduces their thickness and begins forming the coil. Hot rolling improves the metal’s strength and refines its structure.
3. Cold Rolling
After cooling, the hot-rolled aluminum is rolled again, this time at room temperature, to achieve the final desired thickness and enhance the coil’s mechanical properties. This stage helps strengthen the coil and improves its finish.
4. Annealing and Tempering
To increase malleability and eliminate internal stresses, aluminum coils often undergo annealing. This heat treatment makes the coils suitable for various forming processes, enabling manufacturers to cater to a broader range of applications.
5. Surface Treatment and Coating
Aluminum coils may be treated with finishes, such as anodizing, painting, or lamination, to improve corrosion resistance, appearance, and durability. High-quality surface treatments enable aluminum coils to withstand challenging environments, including marine and industrial settings.
Types of Aluminum Coils Offered by Manufacturers
Different applications require aluminum coils with specific properties, and manufacturers typically offer several types based on alloy composition, temper, and treatment. Here are a few commonly produced types:
- 1050 Aluminum Coil: Known for its high purity and excellent corrosion resistance, it’s often used in chemical and electrical applications.
- 3003 Aluminum Coil: An alloy containing manganese, this coil is highly corrosion-resistant and easy to form, making it ideal for packaging and cookware.
- 5052 Aluminum Coil: Known for its strength and high resistance to marine environments, this alloy is popular in marine and automotive applications.
- 6061 Aluminum Coil: A versatile alloy with great mechanical properties, often used in structural applications.
- 7075 Aluminum Coil: High-strength aluminum coil typically used in aerospace and military applications.
Each type is engineered for specific applications, so reputable manufacturers provide a range of alloys and customizations to meet diverse project requirements.
Key Industries and Applications for Aluminum Coils
Aluminum coils are an integral part of multiple industries, each requiring specific qualities and standards from their aluminum materials.
1. Construction and Architecture
Aluminum coils are widely used in construction due to their corrosion resistance, lightweight, and aesthetic appeal. They’re applied in roofing, facades, ceiling panels, and HVAC ducts, where durability and appearance are essential.
2. Transportation and Automotive
In the automotive and transportation sectors, aluminum coils contribute to fuel efficiency by reducing vehicle weight. They are used in body panels, heat exchangers, and even parts of electric vehicle batteries.
3. Aerospace
Aerospace applications demand materials with high strength-to-weight ratios and exceptional durability. High-quality aluminum coils, especially in alloys like 7075, are crucial for aircraft skin panels, wings, and fuselage components.
4. Electronics and Electricals
The high thermal and electrical conductivity of aluminum makes it ideal for applications in electronics, power cables, heat exchangers, and radiators, where efficient heat dissipation is needed.
5. Packaging
Aluminum coils are a primary material in packaging, especially for food and beverage cans. Aluminum’s non-toxic properties and recyclability make it an eco-friendly option for packaging.
What to Look for in an Aluminum Coil Manufacturer
Choosing the right aluminum coil manufacturer can significantly impact the quality, reliability, and performance of the final products. Here are key factors to consider:
1. Quality Standards and Certifications
Manufacturers that adhere to strict quality control and are certified by standards such as ISO 9001 (quality management) and ISO 14001 (environmental management) assure that their aluminum coils meet industry standards and regulatory requirements.
Read also: Why Is Outsourced CTO Expertise Essential for Startups?
2. Range of Products and Customization Options
A reliable manufacturer offers a variety of aluminum coil types, thicknesses, and finishes. Customization options, such as cut-to-length, coil slitting, and surface treatments, are essential for projects with specific requirements.
3. Consistent Supply and Efficient Logistics
For industries dependent on timely material deliveries, a manufacturer’s ability to maintain consistent inventory and reliable logistics is critical. A good supplier offers dependable delivery schedules and can handle both small and large volume orders.
4. Pricing Transparency and Cost-Effectiveness
Transparent pricing and competitive rates are important, but cost should not compromise quality. The best manufacturers offer clear quotes without hidden fees and maintain fair pricing by streamlining production and minimizing waste.
5. Technical Support and Expertise
Leading manufacturers often have in-house technical experts who can provide guidance on material selection, application suitability, and technical details to ensure aluminum coils meet all project demands.
6. Sustainable and Environmentally-Friendly Practices
Manufacturers that employ sustainable practices, such as recycling scrap aluminum and reducing energy usage, align with eco-conscious industries. Aluminum’s recyclability contributes to a lower carbon footprint, and suppliers committed to environmental responsibility are valuable partners for companies with green initiatives.
Conclusion: Finding the Right Aluminum Coil Manufacturer
Choosing the right aluminum coil manufacturer is essential for projects across industries, from aerospace to packaging. Reliable manufacturers provide quality products, customization options, and consistent supply chains, ensuring client satisfaction and project success. By partnering with a reputable aluminum coil manufacturer, companies can secure durable, high-performance materials tailored to their specific needs.
A successful project starts with quality materials, and with the right aluminum coil manufacturer, companies can expect on-time delivery, technical support, and products that meet rigorous industry standards. Aluminum coils remain a cornerstone of innovation, and the best manufacturers help make that innovation possible.